SKF INDIA LIMITED PUNE
“Productivity Improvement at Channel Group 1 from 7000 Bearings/Day to 12000 Bearings/Day for two bearings types”
Project implementation start and end date:
Is it in continued operation now? Yes
Innovation: Elaborate in detail as to how your project stands out for its uniqueness / innovation
A] Consistent achievement of greater than 30% cost saved for 2 product types
- 1.Without any investments in infrastructure.
- 2.Without any direct material cost reduction.
B] Both product types have already registered higher sales
- 1.Product type 1 sale increased by 60% in volume
- 2.Product type 2 sale increased by 60% in volume
C] Additional capacity created leading to sales growth
- 1.Both Product type sale increased to 45 k per month.
D] Process Innovations
- 1.Standardization for the process of Holistic cost reduction that can be replicated across SKF Globally
- 2.Development of innovative process steps for improving performance of machines
- 3.Process innovations like kinetic energy transformation DOE for grinding
- 4.Process innovations like kinetic energy transformation honing process parameters.
- 5.Sequential analysis for vibration scrap reduction
- 6.Simulation DOE
E] Sustainability
- 1.Reduction in energy loss in grinding and honing by utilizing innovation idea of kinetic energy transformations
- 2.Setup chart validated and incorporated in PLC and parameters lock to reduce man machine intervention.
- 3.Training to all concerned employees completed across channels
Problem identification: Why was this problem selected?
What methodology was adopted to identify the problem?
- 1.Business Threat of 20 MINR
- 2.Selling Price of Bearing type 1 was 99.34 INR ,Standard cost of bearing was 100.88 INR, Actual Manufacturing cost was 148.8 INR, Competition was capturing market share for this type due to cost and capacity threat to the tune 1,00,000 brgs per year 10 MINR per year .
- 3.Selling Price of Bearing type 2 was 98.55 INR ,Standard cost of bearing was105.09 INR, Actual Manufacturing cost was 124.8 INR, Competition was capturing market share for this type due to cost and capacity threat to the tune 1,00,000 brgs per year 10 MINR per year .
- 4.Low productivity leading to Non Profitable business & Loss to channel financial parameters

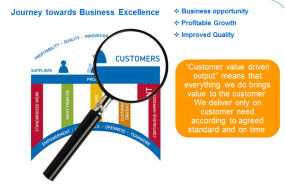
1.Roadmap for productivity improvement & cost reduction started with Structured approach of Standard Cost Break up from Cost controller .
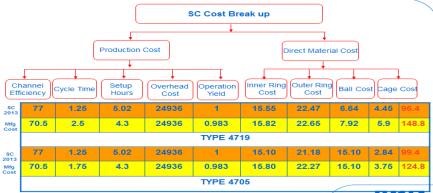
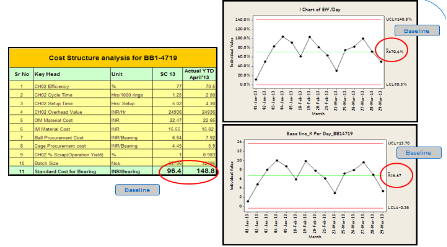
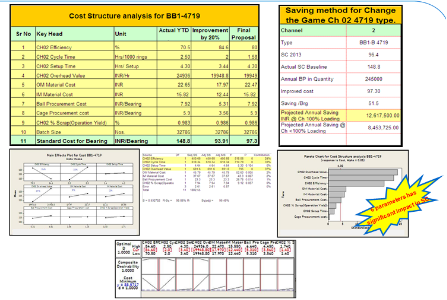
1.From Data collection and sensitive analysis 6 critical components were identified for further improvement An Integrated project management system with structured approach involving all channel management was used to ensuring timely completion of project activities
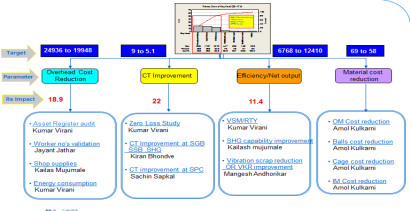
Use of Simulation tool for futuristic bottleneck discoveries coupled with Zero Loss study analytical tool with real time study to identify Cycle time loss machine ,Stoppages , Hidden output losses
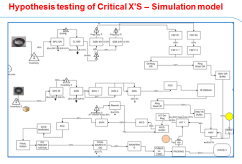
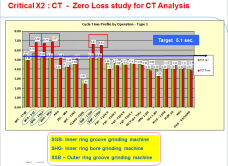
- Analytical Technique of Sequential analysis for improving quality of bearings developed and deployed involving operators
- This is very effective tool which builds a strong cause and effect relationship and contribution of each signification cause to effect via regression
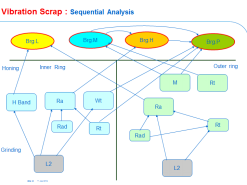
5.Technique of optimizing honing parameters based on kinetic energy transformation and RSM (DOE)
Implementation: How was the chosen solution tested/validated and implemented?
A} FIRST CRITICAL X ….OVERHEAD COST REDUCTION:
Detail analysis was done categorically to understand Overhead cost parameters and which are important as seen in Pareto .
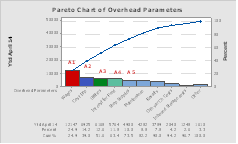
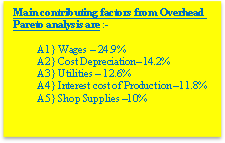
As Per Pareto first priority was to analyse and reduce wages cost ,Wages was analysed in terms of no of fix workmen and flexi workmen and their actual reporting channel ,Allocation of workmen was done on basis of their actual working channel .Possibility of Reduction of manpower was seen as per value addition and recommendation was given.
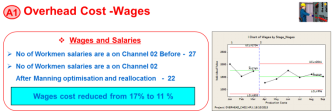
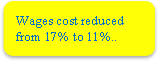
Second Priority was Cost of Depreciation. Assets on Channel having written down value were verified for their availability on channel and were keened machine wise item wise and removed from asset register or reallocated to appropriate

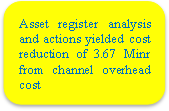
A} FINAL OVERHEAD COST REDUCTION After Analysis and action of overhead key parameter results show reduction in overhead cost
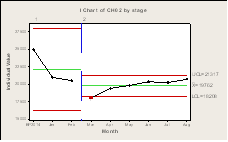
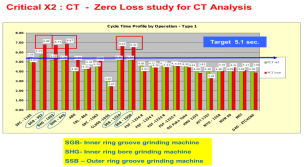
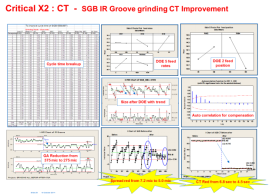

SHG IR Bore grinding machine
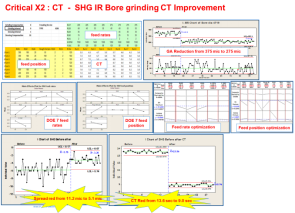
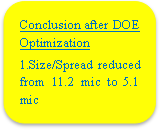
SSB Outer ring groove grinding machine
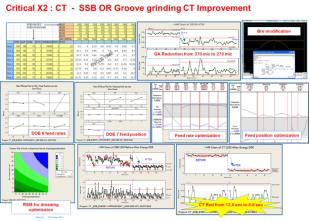
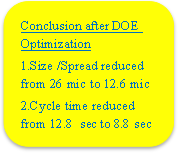
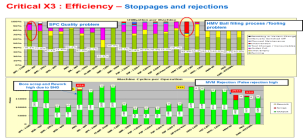

After Geometric alignment of machine Complete Kinetic Energy DOE was conducted for Feed position factors optimization ,Feed rate Factor optimizations and RSM DOE for Dressing parameter optimizations
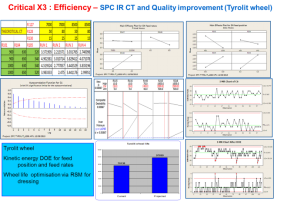
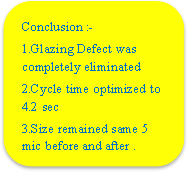
After Detail analysis ..Grinding allowance and Groove Radius allowance was found to be important parameter affecting wheel quality and ring quality ..
Grinding allowance & Radius modified and rings as per new drawing were procured for trials
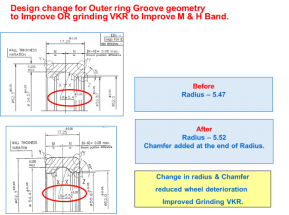

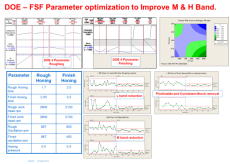

a) Operational benefits:
Sr No | Parameter | Benefit |
1 | Productivity
|
Channel productivity improvement for two types from 7000 bearings/day to 12000 bearings/ day |
Cycle time reduced from 9 sec to 5.4 sec | ||
Sales increased from 28000 to 45000 bearings/month for both types | ||
2 | Machine Availability | · Machine Adjustment and stoppages reduced from 4% to 1% · Spindle Failures eliminated |
3 | Quality | Vibration Scrap reduced from 10% to 2% |
Bore scrap reduced from 3% to 0.5% | ||
Pairing capability improved | ||
First time yield improved from 90 to 98% | ||
4 | Safety | Operator fatigue reduced |
5 | Morale |
b)Financial benefits:
Sr No | Parameter | Benefit |
1 | Cost | Cost per bearing reduced from 148.8 Rs to 98.3 Rs |
2 | Profitability | Financial benefits to organization 23,000,000 Rs./annum |
Institutionalization and horizontal deployment, if any:
Please elaborate on how the changes have been embedded in the system and horizontally deployed as applicable.
Umbrella Project Launched Across Channels of DGBB Pune on Different channels as per Customer Threat and Business Volume