Productivity improvement in BDN Nozzle manufacturing line
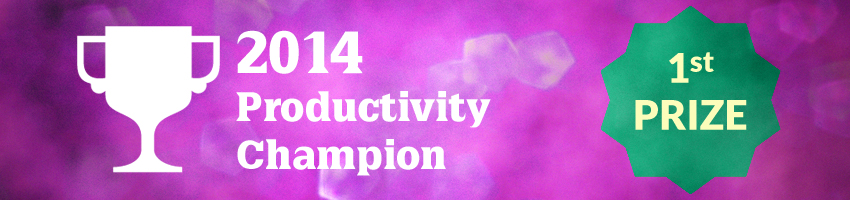
Title: Productivity improvement in BDN Nozzle manufacturing line to meet the sudden increase in customer demand (TML Passenger car and LTV market).
Company: Delphi – TVS Diesel systems Ltd
Project initiation date: 10/10/2012
Challenge
Productivity improvements are the need of hour for the BDN nozzle manufacturing line to meet the sudden increase in customer demand from 2800 nos / day to 4000 nos / day . Current capacity of the line is 3000 nos / day. To meet the increased customer demand it requires investment around 4 crores and also high lead time ( 12 months ) for procurement of new machines. Hence planned to increase the capacity without investment through productivity improvements to meet the increased customer demand.
Also used the takt time vs capacity analysis to identify the above problem.
Data Collection
Following data was collected to understand the current status.
- Customer demand month wise
- Process flow
- Current capacity of each process
- Up time of critical machines
- Rejection levels in each process
- Current manufacturing system
- Current state of layout
- Used the lean manufacturing methodology to collect the data like VALUE Stream Mapping, Cycle time study, Material flow – Sting diagram, Trend graph, Histogram/paretto
Analysis and Solution Development
BDN nozzle manufacturing process consists of 2 stages. Each stage has several sub processes. We have drawn the VSM for each stage to identify the bottle necks in the flow.
Figure 1
Figure 2
The following bottlenecks were identified in the BDN nozzle-manufacturing stream Cycle time is higher than takt time in ECM process
More unwash rejections observed in seat forming process at soft stage resulting FTPR low in downstream processes
Concentricity and linear dimensional issues in OD grinding operation resulting FTPR low in downstream processes.
Up time low in SEIKO ID grinding operation
Batch type production and process type layout is followed in hard stage machining leads to
More material movement
More operator movement for inspection
More handling – re handling
More WIP between process
Difficulties in day-to-day planning
More supervision required
Due to the above constraints it was unable to meet the increased customer demand.
Solution
To eliminate the above listed constraints developed the various ideas through CFT approach as below.
Figure 3
Implementation
Figure 4
Figure 5
Figure 6
Figure 7
Figure 8
Cellular layout formed by physical arrangement of machines according to the process flow.
Single piece flow between each process, material handling system modified, dedicated inspection facility provided, dedicated team formed from various functions and training given to the team about cellular concepts
Sustain
Have standardized the actions taken to sustain the results through Control plan, Operation layout, Drawing Machineries layout document and Engineering change request / process change request
Benefits
Figure 9
Elimination of working on Sundays resulted in power units saving – 60000 units/month and manpower saving - 20 people/day
Financial benefits
Figure 10
Total cost saving/year - 1.51 crores and investment for new machine – 4 crores avoided
Horizontal deployment
Learning of cellular layout concept with single piece flow can be adopted for pump manufacturing stream.
Learning of hard turning operation implemented in pump delivery valve OD turning process.
Other inputs
The team implemented cellular layout with the centralized coolant tank and chillers outside the air condition room which helped in creating dust, mist and fumes free environment (EOHS improvement). Operators are voluntarily coming to work in the newly formed layout and also information flow between customer and supplier process is improved. There is substantial increase in morale of workmen in entire nozzle manufacturing stream.
Figure 11