TOYOTA KIRLOSKAR AUTO PARTS. (Winner)
PRODUCTIVITY IMPROVEMENT IN TRANSMISSION (T/M) ASSEMBLY LINE THROUGH “JISHUKEN” & “LOW COST AUTOMATION (KARAKURI)”
Need for Project
TKAP Business need: T/M Volume Trend
TKAP Labour Cost Trend
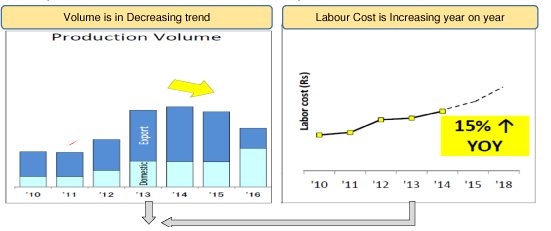
Impact on Product Cost
TKAP Product Cost Target
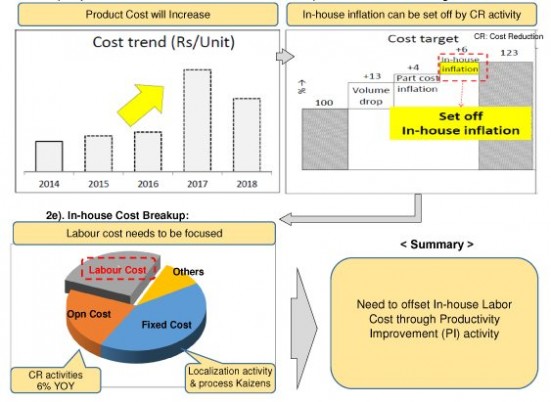
Approach
Conventional Methodology for Productivity Improvement (Labour Cost): Automation
Our Philosophy (Concept)
Effective utilization of Man hour: Increase Value Added work by Reducing Muda (Waste) &
Supplementary work for Productivity Improvement
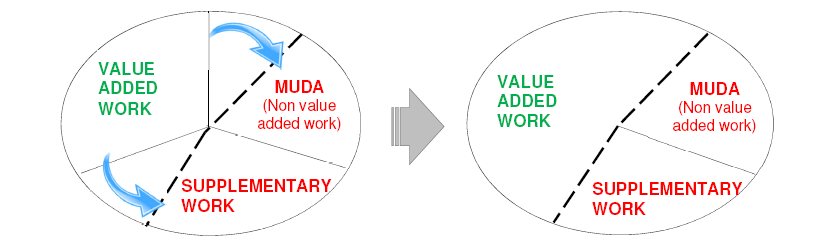
Our Thinking Way: Collaboration of of Jishuken & LCA for increasing the Value Added Work (reduce CT)
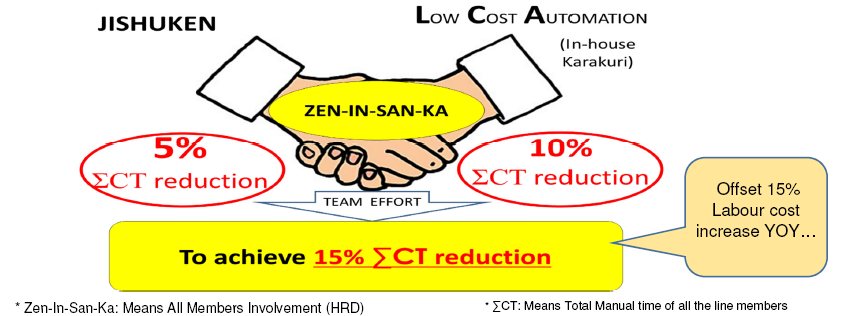
Project Planning
Case Study: T/M Main Assembly & Tester line Productivity Improvement activity
Project Target: 15% Productivity Improvement through CT Reduction (Man loop reduction)
Project Implementation*
* Project implemented from July’14 to Jan’15 (6 Months)
It's a Japanese word which means "Self Learning to improve Self (HRD) & Workplace by Eliminating 3M's."
Objectives of Jishuken:
i) Enhance problem solving skill by teamwork
ii) Productivity improvement by Tackling and Eliminating 3Ms
iii) Promote TPS skill up (HRD of Members)
Jishuken Implementation
Project Implementation
What is Low Cost Automation (LCA) – TKAP Definition..?
A System where Man & Machine Collaborate & Work together (No Separation), which meets Expectations of Toyota Way.
TKAP tool for LCA : "KARAKURI"
What is KARAKURI?
It's a Japanese word which means "Achieving motion with No Power or Low power (use counter weight,
rope & pulley mechanism).
Why KARAKURI?
Low Cost Automation (LCA) Implementation
Challenge: Conventional Automation V/S TKAP Low Cost Automation (Karakuri)
LCA Innovation & Breakthrough Ideas: After Implementation (in continuation with Jishuken)
Types of Karakuri at TKAP
Competitiveness Sustainability through Innovation & Continuous Kaizen