Lucas TVS Ltd
RAMP-UP OF SGM25 (Sundaram Gear Reduction Motor)
Project implementation start and end date:
19.9.2014 to 26.11.2014
Is it in continued operation now? Yes
Innovation: Elaborate in detail as to how your project stands out for its uniqueness / innovation.
- Sudden increase in customer demand for LD-GRS platform1.0 lit starter motor, needing augmentation of capacity by 2-times of the current level the capacity enhancement done by leveraging on the In-house experience, competency and talents. Innovative ideas implemented in all the key cells of the starter motor manufacturing value stream.
Armature line improvements:
- Plan and control to optimize flow in Armature manufacturing cell (Heijunka-leveled production) adopted (Result Armature line balancing output increased by 15%)
- Innovative methods adopted in core pack lamination tool design to improve the input imbalance of the core pack and reduce the final rejection in Armature manufacturing (Result : Armature output increased by 30 % )
- “MTTR” improved in armature manufacturing Dynamic balancing machine and conductor fusing machine by upgrading the control system (both hardware+software). (Result: Down time of both the machines were reduced & MTTR improved from 45min to 3.2 min system up gradation also helped to reduce the cycle time by elimination of additional station(Audit station) in the operation sequence )
- Cycle time reduction in one of the critical bottleneck stage armature core and commutator machining operation by upgrading the special cutting tools and re-design of tool layout.
Yoke & Sub-assembly line improvements:
- SMED concept implemented in Yoke, Armature & Sub-assemble manufacturing cell to minimize losses due to change over time (Armature line equipped with 80% one-off critical capital intensive machines )
- Engineering solution arrived for final performance testing of starter motor to de-bottle necked (Result: Cycle time reduced 38 sec to 27sec.Hence output increase by 20%).
Problem identification: Why was this problem selected? What methodology was adopted to identify the problem?
Customer has come with sudden volume ramp-up increased by 100% in SGM25 starter motor assy from 800 no’s to 1600 no’s/day. But the current capacity was 1086 nos in Armature assembly which is the lowest capacity module among the all sub-assemblies.
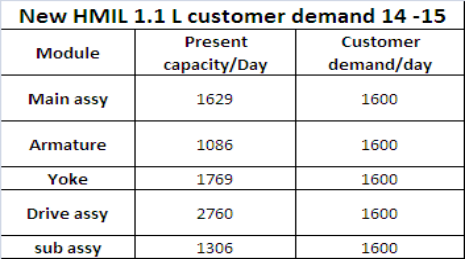
- Some of the Critical process in sub assemblies were identified as bottleneck stations
- Down time and MTTR in Armature assembly is high
- Product change over time is high in Armature assembly.
- Imbalance rejection in Armature assy is high
- Disruption of workflow in armature assy brown stage
Tools and Techniques used:
- TAKT time analysis – To identify bottleneck stations
- Time study – Used stopwatch to take COT study
- Bar graph – Imbalance rejection trend
- Down time study and analysis – To reduce MTTR
- HEIJUNKA - Flow line study
Task force was formed to do productivity improvements in all modules to meet the customer demand with less investment in a short period of time
Data collection: What data was collected? What methodology was adopted to collect the data?
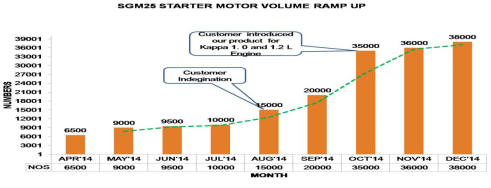
- Demand increase due to localization of starter motor & new product volume increase in the market.
Identification of process measures:
We have done “TAKT” time analysis and time study for all sub assemblies & main assemblies to identify the bottleneck station to do productivity improvements
Tools and Techniques.
- Takt Time study.
- SMED and Cycle time study
- Rejection trend analysis .
- Downtime & MTTR analysis in Armature balancing machine.
Comprehensiveness of data collection:
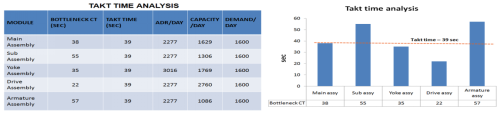
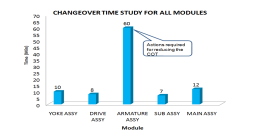
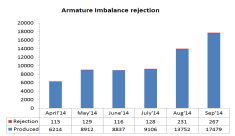
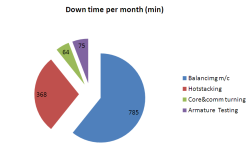
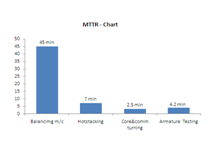
- We checked imbalance value in every stage and found not much variation. So we tried to reduce the initial imbalance of input component by restricting the sheet metal thickness variation and optimizing the pitch setting of lamination blanking tool
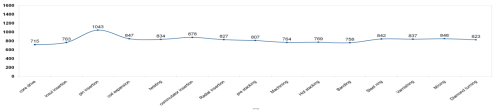
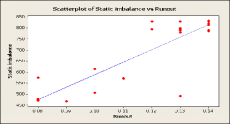

- Reduction of both cutting & non cutting time was planned in Core & Commutator OD turning process. Peripheral activity timing was reduced (51 to 38 Sec) & improved insert with sharper geometry was chosen to reduce double pass (38 to 30 Sec).
- In output shaft bush and pin assy, while doing bush and pin pressing in single station auto loading of bush and indexing of tool takes more time. So we separated both operations
- In performance test rig, 10 times cranking was done against the spec of 5 times for our product endurability. After having consistency in performance, we decided to reduce cranking cycles with approval of product Engineering and quality assurance.
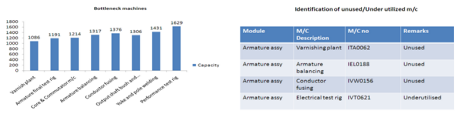
- Among the four underutilized machines, varnish plant was upgraded and the other three were tooled up to suit SGM25.
- SMED - QCT tooling’s planned for Core assy, Conductor twisting and Radial insertion machines which are having more COT
- Input imbalance of corepack was correlated with Face out and R/O and it was reduced by pitch setting. Commutator imbalance was reduced at supplier end by optimizing the process parameters in manufacturing. Where the rejected corepack and commutators were reworked and we can use it.
- MTTR analysis – Balancing and Hotstaking m/c were selected to reduce MTTR .Introduced upgraded hardware unit in balancing m/c and pressure switch for ensuring the collet clamping in Hotstaking
Implementation: How was the chosen solution tested/validated and implemented?
(1) Developed sheet metal thickness variation within 5 microns was tried out to reduce face out of the component within 0.2 mm. We checked 1000 no’s for initial imbalance and found 98.45 % of the core pack are below 500 mg. The rejected corepack were reworked by machining the core OD to reduce CE, DE and Static imbalance.
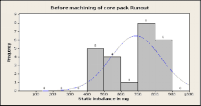
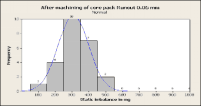

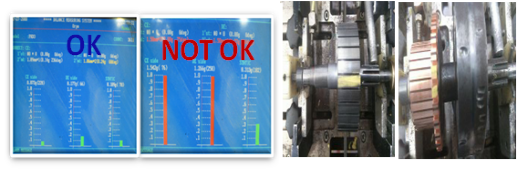

In Hot staking, clamping of component feedback taken from proximity sensor. Due to ineffectiveness in sensing, interruptions were observed frequently.
SMED – QCT provided in three m/c and COT was reduced from 60min to10 min
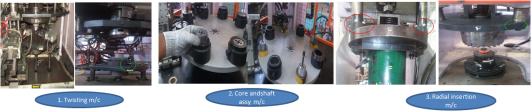
Operational benefits: What benefits were accrued to the organization as a result of the implementation of the project?
- Customer satisfaction by enhancing the capacity from 800/day to 1600/day in shortest possible lead time.
- Support export market to realize a sales value grown up to Rs66.0 lakhs/month (New business)
- Savings Thro’ productivity improvements; 30 % Increased
- a.Manpower reduction 15 man .(optimize the armature flow line improvement done ,Cycle time reduction (core OD turning, Conductor fusing and Performance testing )
- b.SMED Applied ,Setting change over reduction doneTools investment cost / consumables cost reduction.
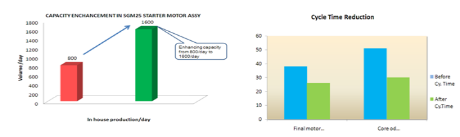
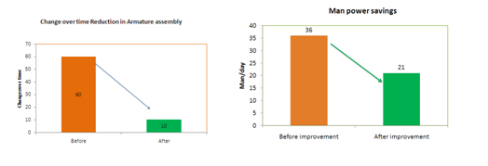
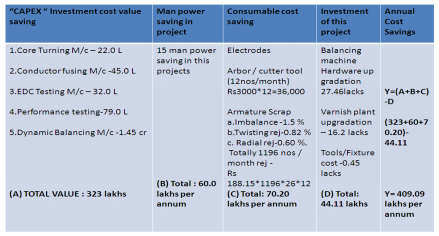
Institutionalization and horizontal deployment, if any:
Please elaborate on how the changes have been embedded in the system and horizontally deployed as applicable
Standardization:
(a). Process change note(PCN) raised for cycle time reduction in core & commutator OD turning and got approved from Quality Manager – Form no.
(b) SOP provided for checking of Core and Commutator imbalance checking and also for reuse of rejected core pack and Commutator after reducing initial imbalance by doing rework.
(c) Component approval made for major tooling, process change and re-establishment of process in underutilized machines – Form no
(d) All the improvements done in this project have been standardized through KAIZEN sheet.
Horizontal deployment:
(a). Same idea in reducing the initial imbalance has been adopted in other varieties like M70 – PRD3, M74 and M70s LTV and successfully we have improved the productivity .
(b) Cycle time reduction in core OD turning process has been going on for the following machines IA0061, IA0049 & IA0057
Contestants may give any other relevant information that can prove helpful to make it a winning entry.
Lamination blanking tool
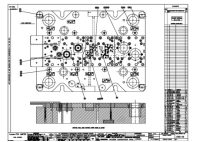

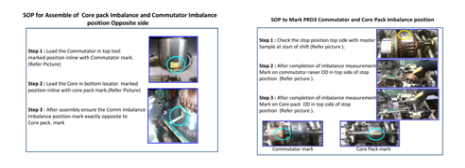